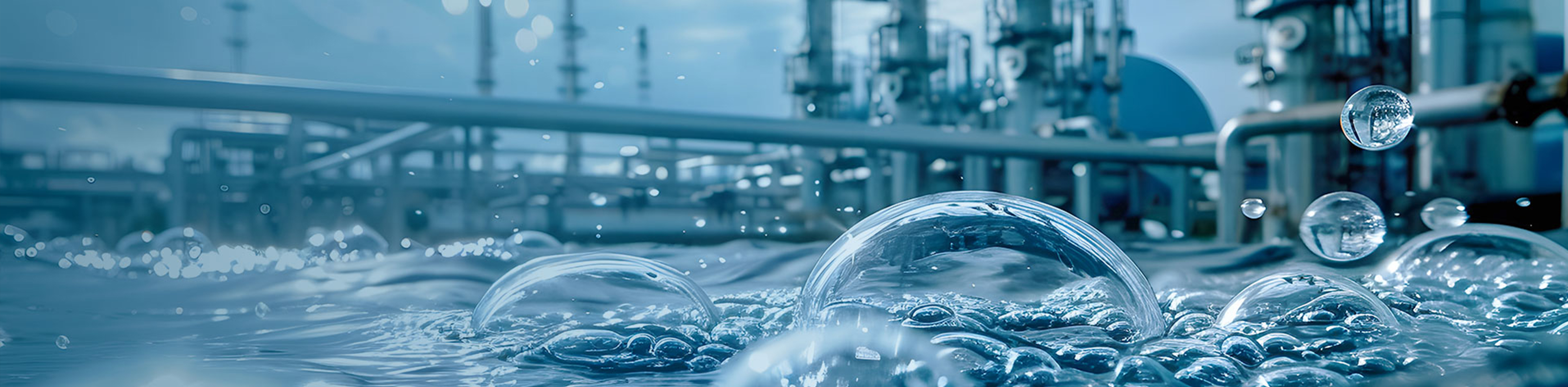
Process Flow Diagram
The boiler blowdown water undergoes treatment through an evaporation system, heat exchange system, multi-media filtration, activated carbon adsorption, and ultrafiltration to remove suspended solids and impurities. Chemicals such as soda ash and phosphate are added to prevent scaling and corrosion, enabling simultaneous water quality stabilization and resource reuse. This reduces equipment wear and extends service life. Through the application of "one-button start" and intelligent technologies, the boiler blowdown wastewater treatment system achieves leapfrog improvements in efficiency, precision, and sustainability.
The wastewater undergoes coagulation and sedimentation pretreatment, combined with ultrafiltration and reverse osmosis membrane separation to purify the water quality, improve circulation efficiency, and achieve energy conservation and consumption reduction. Through the above processes, the wastewater from the power plant's circulating water system can achieve resource reuse and efficient pollutant removal. The comprehensive cost is controllable, and the environmental benefits are significant. This is an important supporting technology for achieving a green power plant.
The treatment process combines coagulation sedimentation and dissolved air flotation to rapidly separate coal powder and suspended solids, supplemented by fiber ball filtration for advanced purification. This approach features high treatment efficiency, coal sludge recovery, reduced turbidity, and water resource conservation, making it adaptable to high-load wastewater characteristics.
The treatment process involves separating floating oil via an oil separator, disrupting the structure of emulsified oil through electrocoagulation, and removing residual oil through coagulation sedimentation and ultrafiltration membranes. This ensures thorough oil-water separation and resource recovery. The treated water can be directly reused or discharged after meeting standards, delivering both economic and environmental benefits. Through data quantification, technical comparisons, and case studies, the advancement and practicality of this high-efficiency treatment technology are systematically demonstrated.
Process 1: Concentrate Volume Reduction + Bypass Flue Gas Evaporation
1. The desulfurization wastewater first undergoes concentration and volume reduction through low-temperature multi-effect evaporation or waste heat concentration, achieving a concentration ratio of over 80%.
2. The concentrated wastewater is then treated by bypass flue gas evaporation, where all water is evaporated. Impurities such as salts are captured by the dust collector along with fly ash in the flue gas.
Process 2: Pretreatment + Electrolytic Chlorine Generation
1. The desulfurization wastewater undergoes pretreatment via coagulation, clarification, and filtration to ensure indicators such as fluoride ions and suspended solids meet the requirements for electrolytic chlorine generation.
2. The pretreated water is mixed with seawater and used as raw water for electrolytic chlorine production, achieving full resource utilization of the desulfurization wastewater.
Process 3: Pretreatment + Salt Separation & Purification + Concentration + Crystallization
1. Pretreatment: Provides high-quality inlet water with reduced turbidity and hardness for subsequent systems, ensuring stable operation and extending system cleaning intervals.
2. Salt Separation & Purification: Utilizes technologies like multi-stage nanofiltration to separate and purify concentrated brine into two main salts: NaCl and Na₂SO₄.
3. Concentration: Employs high-pressure membranes, electrodialysis, etc., to concentrate salts, reducing the treatment volume for crystallization and lowering investment costs.
4. Crystallization: Uses technologies such as MVR (Mechanical Vapor Recompression) and freeze crystallization to convert NaCl and Na₂SO₄ into solid industrial salts.
Technical Reserve
Centered around evaporation crystallization technology, the system covers the entire "pretreatment-concentration-crystallization" chain, integrating highly corrosion-resistant components and intelligent algorithms. It achieves a wastewater recovery rate of ≥95% and crystalline salt purity of ≥98%, leading the industry in technical indicators.
1、High-salt concentration technologies: DTRO membrane (recovery rate ≥85%), evaporator (titanium alloy material, resistant to Cl⁻ corrosion);
2、Pretreatment processes: pre-sedimentation tank, three-compartment tank (pH/ORP precise control), clarifier;
3、Intelligent control: AI dynamic chemical dosing (significantly reduces chemical costs).
Industrialization Advantages
The modular design shortens the delivery cycle to 120 days and effectively reduces the costs of independent processing and operation and maintenance of key components.
1、Rapid Delivery: Modular design + standardized production + digital collaboration;
2、Cost Advantages**: Global supply chain layout + global advanced intelligent processing equipment + computer-aided AI design;
3、Closed-Loop Service: Full lifecycle operation and maintenance (AI remote monitoring, substantial reduction in O&M costs).
Related products